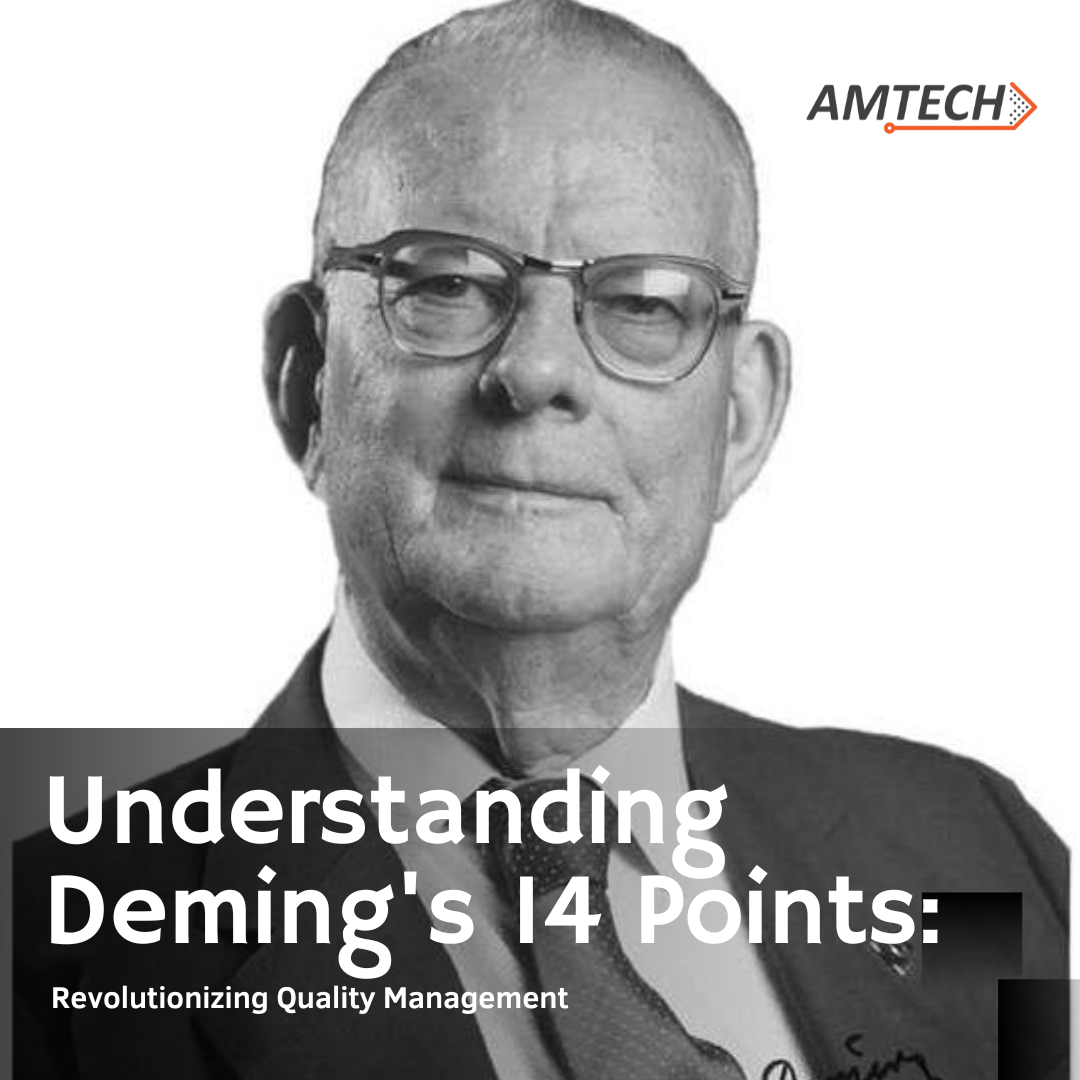
Quality management has long been a cornerstone of successful businesses, aiming to enhance products, processes, and overall organizational effectiveness. And at Amtech, we are no exception. In the pursuit of excellence, numerous methodologies have been developed, each contributing to the evolution of quality practices. Among these, Dr. W. Edwards Deming’s “14 Points” stands as a pioneering framework that revolutionized quality management across industries.
Who was W. Edwards Deming?
W. Edwards Deming (1900-1993) was an eminent statistician, engineer, professor, and management consultant whose principles transformed the landscape of quality control and organizational management. Born in the United States, Deming is notably recognized for his significant contributions to Japan’s post-World War II economic recovery and the subsequent global dissemination of his philosophies on quality.
The Essence of Deming’s 14 Points
Deming’s 14 Points are a set of guiding principles aimed at transforming the way organizations approach management and quality. These points, encapsulated in his book “Out of the Crisis” published in 1982, serve as a blueprint for achieving operational excellence and fostering a culture of continuous improvement. Let’s delve into these principles:
1. Create constancy of purpose toward improvement
Organizations should establish clear, unwavering objectives focused on continuous improvement, innovation, and meeting customer needs.
2. Adopt the new philosophy
Embrace a new mindset where quality and improvement are not mere afterthoughts but integral aspects of every process and decision within the organization.
3. Cease dependence on mass inspection
Move away from the traditional reliance on final inspection to catch defects and errors and instead emphasize building quality into the production process itself.
4. End the practice of awarding business based on price tag alone
Understand that selecting suppliers based solely on price can compromise quality. Long-term relationships founded on quality and mutual benefit are crucial.
5. Improve constantly and forever the system of production and service
Strive for ongoing enhancement in processes, products, and services to stay ahead in an increasingly competitive market.
6. Institute training on the job
Invest in continuous training and skill development to empower employees and enable them to contribute effectively to quality improvement.
7. Institute leadership
Effective leadership is essential in fostering an environment that encourages innovation, teamwork, and continuous improvement.
8. Drive out fear
Create an atmosphere where employees feel safe to voice concerns, suggest improvements, and take calculated risks without the fear of reprisal.
9. Break down barriers between departments
Encourage collaboration and teamwork across departments to optimize processes and achieve common organizational goals.
10. Eliminate slogans, exhortations, and targets for the workforce
Replace arbitrary goals with a deeper understanding of processes and focus on quality improvement rather than setting unrealistic targets.
11. Eliminate numerical quotas
Quotas often lead to suboptimal quality and demotivation. Focus on improving processes to achieve quality outcomes instead of imposing arbitrary targets.
12. Remove barriers to pride of workmanship
Cultivate an environment that nurtures pride in workmanship by recognizing and appreciating employees’ contributions.
13. Encourage education and self-improvement for everyone
Support continuous learning and personal development for all employees, fostering a culture of growth and adaptability.
14. Take action to accomplish the transformation
Implement these principles consistently and wholeheartedly, recognizing that transformation requires dedication, persistence, and systematic change.
The Enduring Legacy
Deming’s 14 Points are highly relevant and influential in building our operation at Amtech. They emphasize a shift from a short-term, profit-centric approach to a more holistic, quality-driven philosophy that values continuous improvement, customer focus, and employee empowerment.
By embracing Deming’s principles, we have witnessed improvements in product quality, customer satisfaction, and overall operational efficiency. By instilling a culture of quality and continuous improvement, we consistently gain a competitive edge in an ever-evolving PCB Assembly marketplace.
Over the next few months, we’ll drill even further into Deming’s 14 Points and share how they have become a guide for us by integrating these principles into our ethos and to benefit customers.